HomeERP for Manufacturing: Enhancing Production Efficiency and Quality Control UncategorizedERP for Manufacturing: Enhancing Production Efficiency and Quality Control
ERP for Manufacturing: Enhancing Production Efficiency and Quality Control
ERP for Manufacturing: Enhancing Production Efficiency and Quality Control
The manufacturing sector has special difficulties in limiting downtime, efficiently managing supply chains, and striking a balance between high-quality output and operational efficiency. In the absence of appropriate technology, these difficulties may become too much to handle. ERP for Manufacturing facilitates departmental integration into a single workflow, real-time production activity monitoring, and process simplification for enterprises. When paired with CRM for Manufacturing, it enables companies to improve customer happiness, establish enduring connections, and increase operational effectiveness. The characteristics and advantages of ERP and CRM systems for manufacturing businesses will be examined in this comprehensive blog.
What is ERP for Manufacturing?
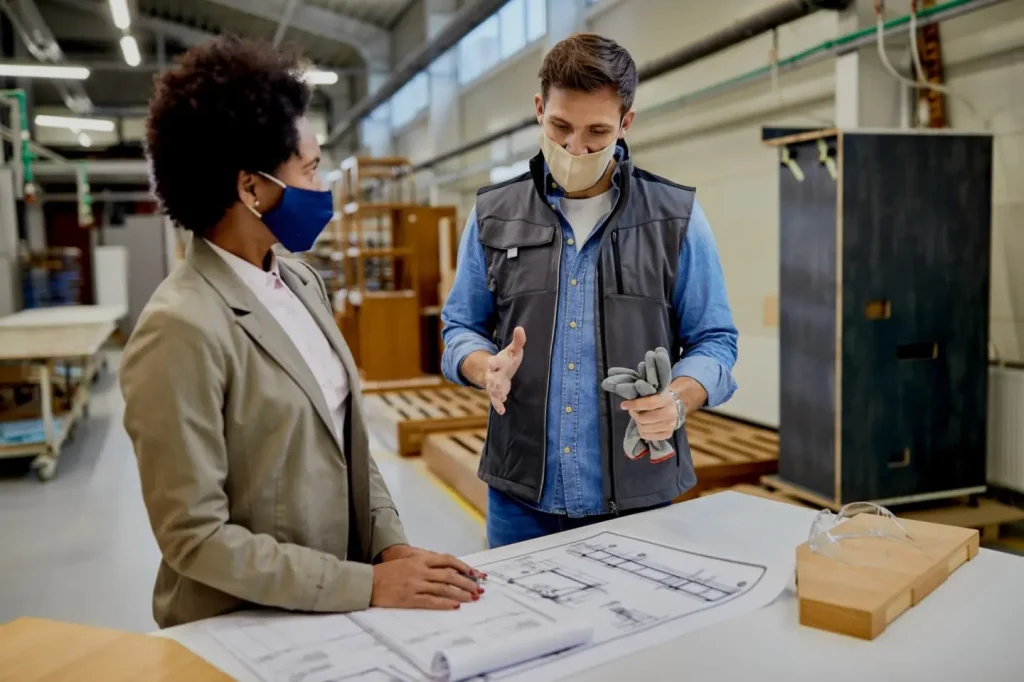
The main business operations of a company, including supply chain management, inventory management, finance, production, and procurement, are all intended to be automated and unified by an enterprise resource planning (ERP) system.
ERP is essential to manufacturing firms because it provides information on production schedules, equipment utilization, and raw material availability. Enterprise Resource Planning (ERP) software guarantees that all manufacturing process elements function together to precisely and effectively satisfy client demands.
Key Features of ERP Software for Manufacturing
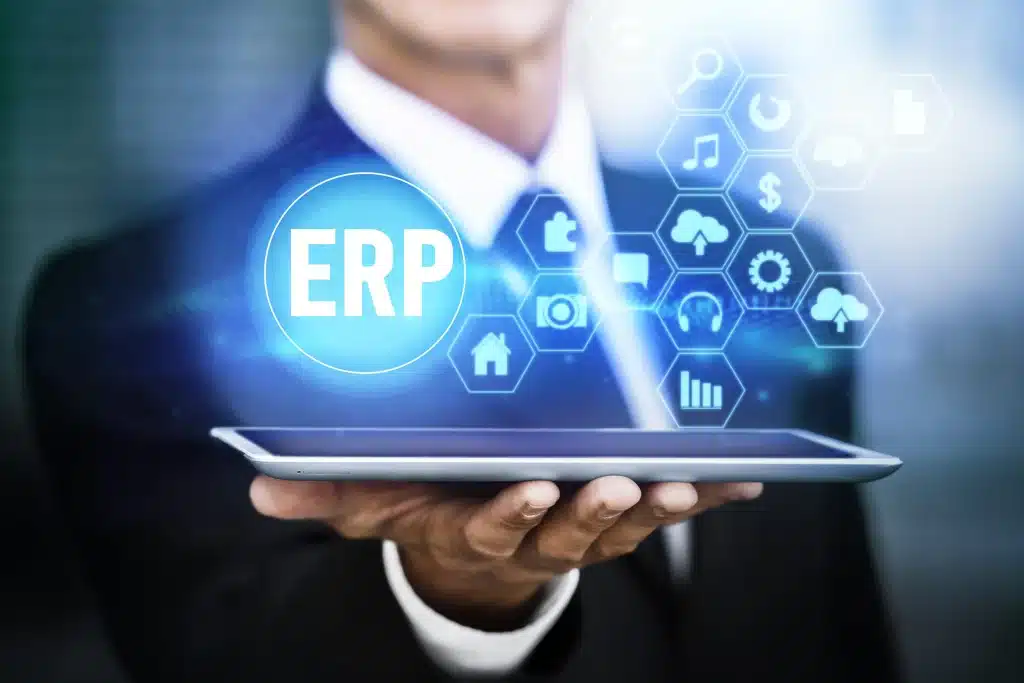
Production Planning and Scheduling
ERP software helps businesses optimize production schedules by tracking raw materials and labor availability. It enables manufacturers to align production with order deadlines, minimizing bottlenecks and enhancing productivity.
Inventory and Supply Chain Management
The system provides real-time inventory tracking to prevent stockouts and overstocking issues. It enhances supply chain coordination by automating vendor management and procurement processes.
Quality Control and Compliance
ERP solutions allow businesses to monitor quality at every stage of production, ensuring products meet regulatory standards. Automated quality checks and alerts help detect errors early, reducing waste and rework.
Financial Management and Reporting
ERP software integrates financial data from different departments, providing a clear overview of expenses, revenue, and profitability. Customizable reports offer insights into production costs and areas for improvement.
Integration with CRM Systems
ERP systems can integrate with CRM software, enabling businesses to manage customer relationships, monitor sales, and ensure on-time delivery. This synergy allows better coordination between production and sales teams, improving customer satisfaction.
The Role of CRM for Manufacturing
A CRM system, which emphasizes customer-centric procedures, is a useful addition to ERP. CRM aids in the efficient management of leads, consumer inquiries, and after-sales support for manufacturers. CRM improves customer happiness and retention when it is connected with ERP because it offers a comprehensive view of customers, including order status and sales history.
Lead and Opportunity Management
CRM helps manufacturers track potential customers and convert leads into sales. By monitoring customer behavior and preferences, sales teams can provide more personalized offerings.
Sales Forecasting and Order Management
CRM software forecasts future demand based on historical data, helping manufacturers align production with market trends. It ensures seamless communication between sales and production teams, preventing delays in fulfilling orders.
Customer Service and Retention
CRM systems enable manufacturers to manage customer complaints, warranties, and post-sales service efficiently. By nurturing long-term relationships, CRM helps retain customers and increase repeat business.
Benefits of ERP and CRM for Manufacturing
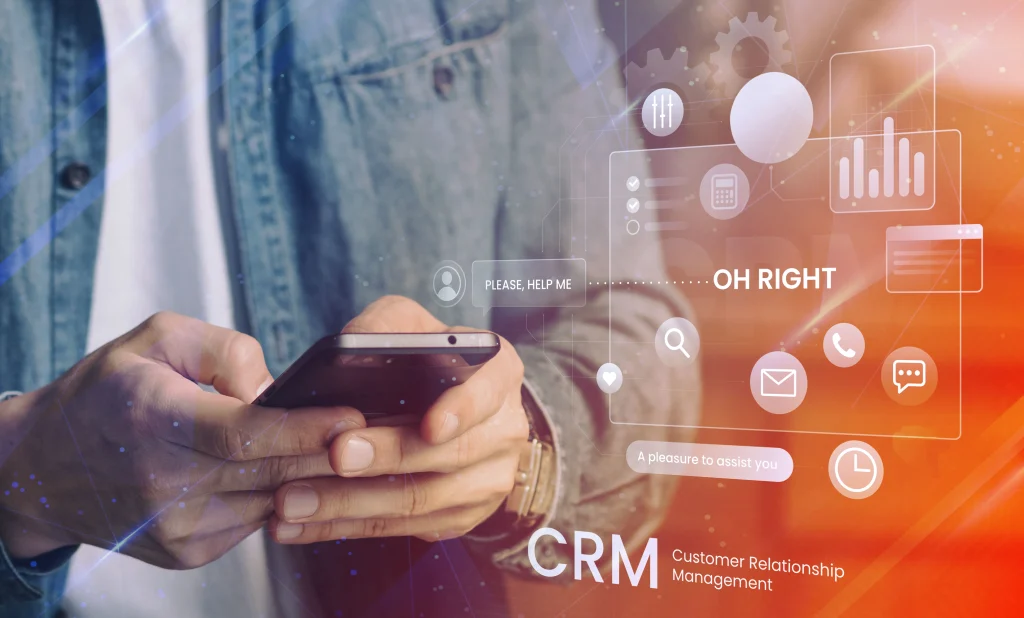
Increased Operational Efficiency
- ERP automation reduces manual errors and accelerates routine tasks like production planning, procurement, and financial reporting.
- CRM integration ensures smooth communication between sales, service, and production departments.
Enhanced Quality Control
- Real-time monitoring of quality parameters ensures that manufacturing processes meet stringent quality standards.
- Early detection of defects reduces the need for rework and minimizes product recalls.
Cost Reduction
- ERP software enables manufacturers to optimize resource utilization, reducing wastage and unnecessary expenses.
- Improved inventory management lowers holding costs and minimizes disruptions in the supply chain.
Improved Customer Satisfaction
- With CRM integration, businesses can track order status, offer timely delivery updates, and handle customer complaints effectively.
- Personalizing communication and services improves customer loyalty and retention.
Real-Time Data and Decision-Making
- ERP provides executives with real-time dashboards, empowering them to make data-driven decisions swiftly.
- Analytics from CRM systems offer insights into customer preferences, helping businesses stay competitive.
Choosing the Right ERP and CRM Software Company: Why ERPONE is the Ideal Partner
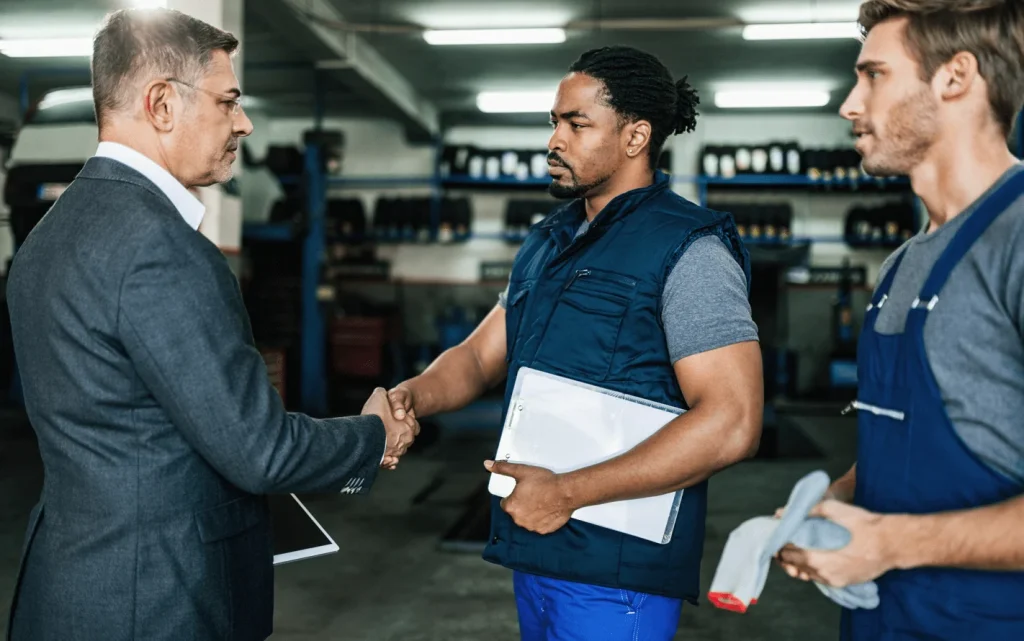
Choosing the best ERP and CRM software provider for your manufacturing firm is an important choice. You require a system that grows with your company in addition to easily integrating with your current workflows. ERPONE specializes in offering ERP and CRM solutions that are specifically designed to meet the demands of manufacturing sectors.
ERPONE is the ideal partner for your digital transformation for the following reasons:
Fully Integrated ERP and CRM Platforms
ERPONE provides end-to-end ERP systems with a single platform for managing finance, procurement, inventory, production scheduling, and quality control. The CRM module seamlessly integrates with ERP, ensuring smooth coordination between sales, service, and operations. This ensures you get a 360-degree view of your business operations and customer interactions in real time.
Customization and Scalability
ERPONE provides custom ERP and CRM software that fully fits your specific business operations. ERPONE offers customized solutions that expand with your company, whether you’re automating processes, monitoring client information, or integrating with legacy systems.
User-Friendly Interface and Cloud Solutions
ERPONE makes certain that its platforms are user-friendly, reducing the learning curve for staff members. Their cloud-based ERP and CRM systems are accessible anywhere, guaranteeing data consistency and real-time changes across sites, a crucial feature for contemporary manufacturing companies with numerous locations.
Dedicated Support and Training
It can be difficult to implement ERP and CRM software, but ERPONE guarantees an effortless transition with professional assistance at every turn. They provide thorough training and continuous customer service to guarantee that the solutions are used to their maximum capacity. ERPONE works together to make sure your investment is profitable in the long run.
Cost-Effective Solutions for SMEs
ERPONE understands the budget constraints faced by small and medium enterprises. Their affordable pricing models and modular ERP and CRM systems allow businesses to scale up the functionality as needed without unnecessary upfront costs. This makes ERPONE a cost-efficient partner for SMEs looking to optimize their manufacturing operations.
Conclusion
ERP for Manufacturing must be used by businesses who want to increase production efficiency and assure product quality. ERP systems assist with streamlining operations and cutting expenses with capabilities like production scheduling, quality control, and real-time monitoring. By ensuring smooth communication between the sales, production, and customer support teams, ERP and CRM integration for manufacturing can increase customer satisfaction and fuel company expansion.